不同钢级钻杆和套管的磨损
不同钢级钻杆和套管的磨损
在进行钻井作业时,钻杆和套管是必不可少的工具,它们的材质和性能直接影响到钻井作业的效率和安全。磨损系数是评价钻杆和套管磨损程度的重要指标之一,不同钢级钻杆和套管钢级的磨损系数直接反映了它们的耐磨性能。为减少因磨损导致的套管失效、井喷、甚至全井报废等事故,国内外学者进行了不同工况条件下套管的磨损试验研究,分析了泥浆成份、工具接头、护箍和泥浆中的砂子对套管磨损的影响,建立了计算套管磨损程度的模型。
套管磨损试验研究方面,前苏联的 Lewis 和 Kiseman 等人最早开始了钻杆和套管之间的磨损研究。Shell 公司的 Bradly,Fontenot 等人采用立式全尺寸套管磨损试验机研究了钻进过程中钻杆的旋转、起下钻和测井钢丝对套管磨损的影响。钻杆旋转钻进过程中套管磨损严重;起下钻和测井钢丝对套管磨损的影响较小;泥浆类型、工具接头类型和砂子对套管磨损影响较大。正压力越大,橡胶护箍减磨作用越明显;正压力小时,橡胶护箍会增加套管的磨损;钻井泥浆中的非磨粒钻井岩屑和重晶石能够减少套管的磨损。新工具接头造成的套管磨损严重,不能在有套管的井中使用。泥浆中的砂子增加套管的磨损,正压力越大砂子的影响越严重,尤其是在清水中套管的磨损更加严重。小尺寸和全尺寸套管磨损试验机上进行的套管磨损试验表明其磨损机理相似,套管磨损表面形成了硬化层,套管试样表面的磨损机理主要有黏着、磨粒和剥落磨损。泥浆类型影响着套管的磨损程度,套管和工具接头表面形成的保护膜能够减少套管的磨损。低密度泥浆中的润滑剂能显著减少套管钻杆试样摩擦副之间的摩擦系数,降低套管的磨损。研究结果表明小尺寸磨损试验机不能模拟现场套管钻杆接头接触的实际情况。Williamson 和 Hall 等人研究了套管钻杆试样摩擦副间接触应力对套管磨损的影响;认为低应力下套管磨损为磨粒磨损,高应力下为黏着磨损,磨损机理的转变有一个门槛值;研究表明增加套管钻杆摩擦副间的接触点能减少套管磨损,小直径钻杆比大直径钻杆磨损套管更加严重,井眼狗腿度对套管磨损的影响较大,井下套管磨损程度与狗腿度之间的关系是非线性的。
高密度钻井液中的磨损试验表明 P110 套管试样的磨损系数随接触正压力的增加而增加,正压力和磨损系数之间是线性关系;套管磨损试验过程中存在一个转速临界值,超过这个值套管磨损程度随转速急剧增加。泥浆中的铁矿粉会加重套管的磨损,套管的磨损机理也会随着铁矿粉含量的增加由磨粒磨损变为黏着和疲劳磨损。重晶石泥浆中进行的套管磨损试验表明随着铁矿粉的增加,套管的磨损先增加后减少;泥浆中铁矿粉和重晶石的配比为 1:2 时套管的磨损最少,如图1所示;随着摩擦副间正压力的增加,套管的磨损机理由磨粒磨损转变为黏着磨损。
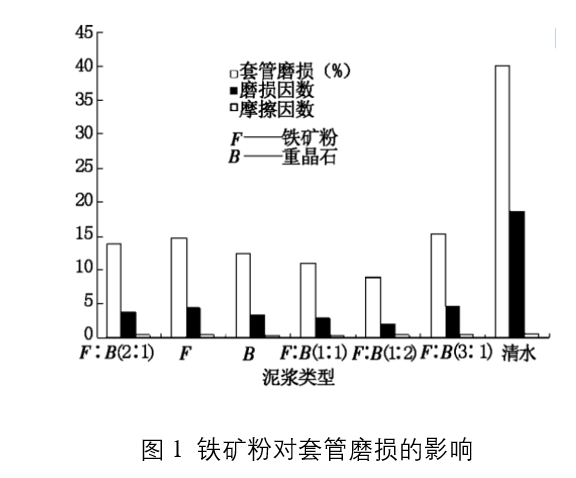
钻井泥浆中的减磨剂对套管磨损的影响较大。钻杆和套管内表面之间的正压力、橡胶护箍、减磨剂以及钻杆接头耐磨带是影响井下套管磨损的重要因素。正压力是影响套管磨损的主要因素,橡胶护箍能够显著减少套管的磨损,泥浆中的重晶石颗粒对套管的减磨效果明显。套管磨损机理与正压力关系明显,高正压力作用下主要发生疲劳、黏着和磨粒磨损;卡瓦材料也是影响套管磨损的主要因素。摩擦副间滑动速度较小时,套管的磨损系数与滑动速度之间是线性关系;钻井过程中钻具组合的振动会增加井下套管的磨损系数。
套管磨损预测研究方面,Maurer和Hall结合现场套管磨损实际情况,给出了CWEAR套管磨损软件中磨损系数的确定方法。目前,油田现场套管磨损预测和计算中采用的磨损系数取实验室测得数值的2倍;提高测井精度和缩小测井间距可以提高套管磨损预测的准确程度;有钻杆护箍存在时套管的磨损系数是没有钻杆护箍时的 1%;短狗腿的存在会导致套管磨损预测数值偏小。White 认为套管内表面材料去除体积与摩擦副表面的摩擦功成正比,比例系数为套管的磨损效率,套管试样表面金属去除体积 :
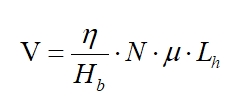
其中:N为钻杆套管摩擦副间正压力,N;μ为摩擦副间摩擦系数,无量纲; Ls 为摩擦副间滑动长度,m;V为套管试样表面金属去除体积,m3;η/Hb为套管磨损效率,
Pa-1。该公式广泛应用于现场井下套管磨损的预测。
White 等人进行了水基和油基泥浆中不同钢级套管的磨损试验研究,给出了水基和油基泥浆中J55、N80 和P110三种钢级套管的磨损系数,如表1所示。钻井手册(甲方)采用该组数据预测和计算井下套管的磨损程度。White 的试验结果表明套管钢级越高耐磨性越差,油基泥浆中套管的磨损系数大于水基泥浆泥浆中的磨损系数,油基泥浆中套管的磨损更加严重。该项研究未考虑钻井泥浆密度的影响,也没有进行试验测量高钢级套管的磨损系数。表中数据不适用于现在深井、超深井套管磨损程度的预测。
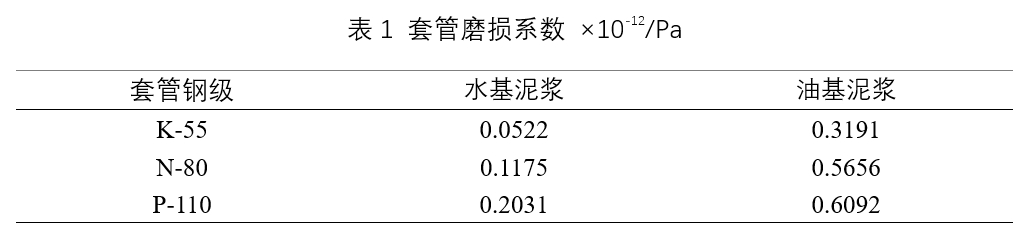
White 的磨损试验中 P110 套管的磨损系数高于 N80 套管的。高钢级套管磨损系数高于低钢级套管的,这一结论的解释是高钢级套管和钻杆接头硬度接近,耐磨性较差;以及制造 N80 套管的钢材耐磨性好。高钢级套管的强度和硬度更高,其耐磨性要好于低钢级套管的。
王小增通过选取油田常用 N80,P110 ,TP140和VM140套管进行磨损试验研究。根据油田实际钻井工况,磨损试验机转速设定为100 r/min ;泥浆密度分别为 1.4、1.8和2.0 g/cm3;套管和钻杆材料试样间正压力分别设定为 200、400和600N。拟采用能量效率模型计算套管的磨损程度。该模型中套管的磨损体积与摩擦副间的滑移速度无关,滑移速度对套管材料磨损程度的影响不在研究范围之内。高温井中井筒温度小于200 ℃,该温度对套管磨损性能影响较小;钻井过程中泥浆循环导致套管和钻杆材料接触面的温度不可控,未考虑温度对套管材料磨损性能的影响得到了钢级对套管材料磨损影响的试验结论。
钻井深度增加导致井筒所受的地层压力和井筒内液柱压力增大,套管内表面磨损严重。套管磨损后壁厚减少、强度降低,需要采用高钢级套管固井来增加其抗挤毁和抗破裂强度,降低井下套管失效风险。高钢级套管的耐磨性能是否高于低钢级套管的需要进行套管材料磨损试验研究。
套管材料试样磨损试验过程中,钻杆和套管材料试样之间的正压力固定在400 N;钻杆材料试样转速固定在100 r/min ;配置的水基泥浆密度是31.4 g/cm 。磨损试验用套管材料试样由 N80,P110,TP140和VM140等不同钢级套管加工而成;钻杆材料试样在S135钻杆上取材。在钻杆套管材料摩擦磨损试验机上进行套管材料磨损试验,实测套管材料的磨损系数和摩擦系数,分析套管钢级对井下套管耐磨性能的影响。为比较套管材料硬度对套管材料耐磨性能的影响,本文实测了磨损试验用套管材料的洛氏硬度。测量结果表明套管材料钢级越高,材料的屈服强度越大,洛氏硬度也越大。
