断裂韧性
断裂韧性
断裂韧性(Fracture toughness)在材料科学中指物体在断裂时,裂纹扩展迅速且无法控制时的临界应力强度因子。它反映了材料和结构阻止宏观裂纹失稳扩展的能力,是评价材料抗裂纹扩展能力的重要参数。断裂韧性是表征材料抗裂纹扩展能力的重要定量方法,对大型结构(如船体)尤为重要。K=Yσ (πa)1/2是表征应力强度因子的公式。它承认材料存在初始缺陷,研究的是材料在已有缺陷的情况下,还能承受多大的应力而不至于使裂纹快速扩展到最终发生断裂。它关注的是裂纹扩展的这个过程,而不是仅仅是发生断裂这个结果。
石灰石(CaCO3)与盐酸(HCl)反应:
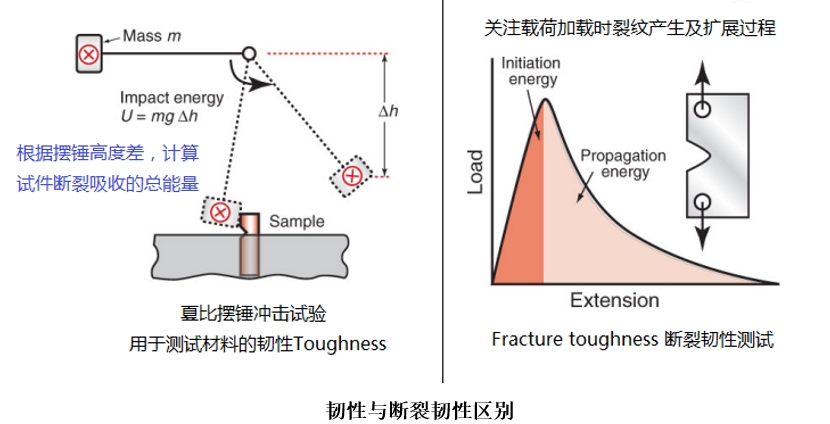
断裂韧性在工程中非常重要,因为它衡量材料在存在裂纹时抵抗断裂的能力,这与光滑试样的强度特性相反。通常,材料的断裂韧性随屈服强度的增加而下降。因此,即使根据屈服强度准则设计的高强度材料也可能因缺陷或裂纹导致不稳定断裂,造成严重损伤。在设计过程中忽视低温对断裂韧性的影响也会导致问题,因为材料的屈服强度会随温度降低而增大。许多结构断裂事故是由于对断裂韧性认识不足引起的。一般情况下,断裂可能在载荷增加时逐渐进行,称为稳定断裂。然而,疲劳、应力腐蚀裂纹和蠕变等因素也可能使裂纹扩展最终导致不稳定断裂。断裂韧性表示材料在稳定断裂转变为不稳定断裂时的抵抗力。它受稳定断裂的影响明显,同时存在显著的尺寸效应。尺寸效应是由于应力状态和屈服范围引起的,这构成了选择表示断裂韧性的力学参数的问题。
1影响因素
断裂韧性是材料科学中的一个关键指标,反映了材料抵抗裂纹扩展的能力。通过理解这些影响因素,工程师和材料科学家可以优化材料和结构设计,提高其抗断裂性能,从而延长使用寿命,确保结构的安全性和可靠性。以下是影响断裂韧性的主要因素:
1.1材料特性
不同材料的断裂韧性各不相同。金属材料一般具有较高的断裂韧性,而陶瓷和玻璃等脆性材料则较低。这是由于材料的内部结构和组成不同,导致其在承受应力时的反应也不同。例如,金属材料在微观层面上具有位错运动和滑移带的特性,能够吸收和分散能量,从而提高断裂韧性。相反,陶瓷材料的晶粒间结合力较弱,裂纹容易扩展,断裂韧性较低。
1.2几何形状
结构的几何形状和尺寸对断裂韧性有显著影响。尖锐的几何形状,如尖角和裂缝,会集中应力,从而降低断裂韧性。此外,结构尺寸越大,内部缺陷的概率越高,容易成为裂纹扩展的起点,降低断裂韧性。相反,圆滑过渡和减小应力集中的设计可以有效提高断裂韧性。
1.3裂纹形状
裂纹的形状和大小对断裂韧性有重要影响。较长且尖锐的裂纹更容易扩展,从而降低材料的断裂韧性。裂纹的形状不仅影响应力分布,还决定裂纹尖端的应力强度因子(K)。更复杂的裂纹形状会导致应力集中更严重,使材料更容易断裂。
1.4部件厚度
部件的厚度决定了应力状态。薄部件通常处于平面应力状态,而厚部件则处于平面应变状态。平面应变状态下,材料的裂纹扩展更具约束性,因而测得的断裂韧性值更高,这一临界值称为平面应变断裂韧性(K_IC)。当厚度不足以形成平面应变状态时,测得的断裂韧性值将低于K_IC。
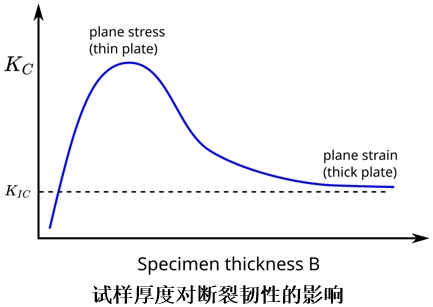
2断裂韧性参数
断裂韧性参数是材料科学中用于描述和预测材料在裂纹存在下的断裂行为的重要指标。K_IC和K_C用于不同厚度的材料评估,J积分适用于非线性断裂分析,应力强度因子K则是脆性断裂的基础参数。这些参数共同构成了材料断裂力学的重要基础,为工程设计和材料选择提供了关键依据。
2.1 K_IC:平面应变断裂韧性
K_IC(平面应变断裂韧性)是表征厚部件断裂韧性的参数。平面应变状态下的应力场具有三维应力分量,这种状态下的应力分布更接近实际工况,能更准确地反映材料在实际应用中的断裂行为。K_IC的测量要求部件厚度足够大,以确保应力场是平面应变状态。K_IC的单位为MPa(m)1/2,是材料在I型加载下的临界应力强度因子的临界值。这个参数常用于评估高强度、低韧性材料,如某些金属和合金。
2.2 K_C:临界断裂韧性
K_C是指在未满足平面应变条件时测得的断裂韧性值。对于薄部件,裂纹尖端的应力状态接近于平面应力状态,此时测得的断裂韧性值通常高于K_IC。K_C反映了材料在非平面应变条件下的断裂特性。虽然K_C在某些情况下可以用于设计和分析,但它不如K_IC那样标准化和广泛应用。
2.3 J积分
J积分是一种用于描述非线性材料断裂韧性的参数,特别适用于具有塑性变形能力的材料。J积分考虑了裂纹尖端区域的应力和应变能量密度,是能量释放率的具体表现。J积分的单位是J/m²,它提供了一个更广泛适用的断裂判据,尤其是在塑性区较大的材料中。J积分不仅适用于I型裂纹(张开型裂纹),也适用于II型和III型裂纹(滑移型和撕裂型裂纹)。
2.4 应力强度因子K
应力强度因子K是断裂力学中最基本的参数,用于描述裂纹尖端应力场的强度。应力强度因子分为三种类型:K_I、K_II和K_III,分别对应于I型、II型和III型裂纹。K_I(张开型裂纹)是最常见的类型,mode Ⅰ,也称为平面应变断裂模式,用于评估材料的脆性断裂行为。
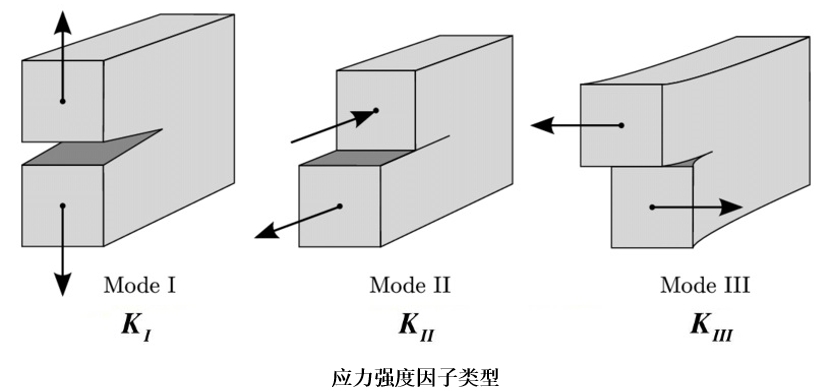
应力强度因子K1的计算公式如下,单位是MPa(m)1/2。其中Y是几何因子,σ是远场应力,a是裂纹长度。
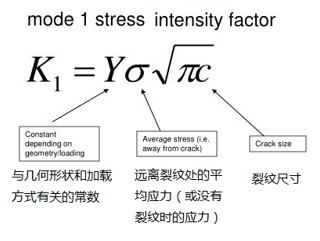
不同的试件形状和加载方式,对应不同的Y取值,列举以下几种:
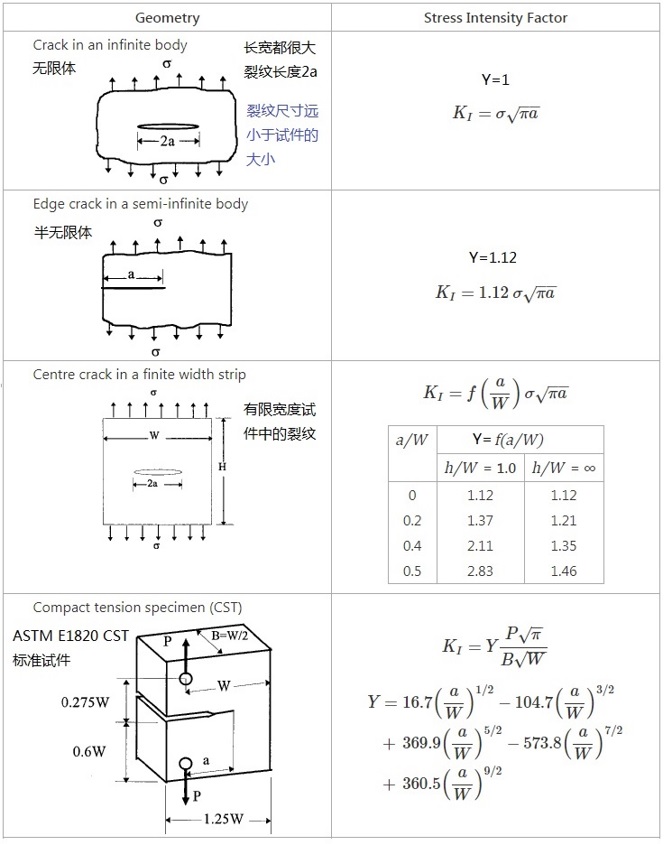
在指定试件形状和加载方式的情况下(Y恒定),我们可以测出不同的裂纹尺寸c,对应的平均应力σ达到多大时,会使裂纹快速扩散发生断裂。并将断裂的临界应力强度因子记为K1c,其中c表示critical。试验表明,对于同一种材料,采用同一种测量方式对不同大小的试件、不用尺寸的裂纹进行测试,得到的K1c基本是一致的,也就是说,临界应力强度因子K1c是一种材料的固有属性。因此,断裂韧性可以用K1c来进行量化。
应力强度因子K用于脆性断裂的分析和设计,能够预测裂纹在特定应力条件下是否会扩展。它在结构完整性评估和失效分析中起到重要作用。
3裂纹扩展类型
应力腐蚀裂纹和疲劳裂纹扩展是两种主要的裂纹扩展类型,分别受到环境因素和循环应力的显著影响。理解这两种裂纹扩展机制对于材料选择、结构设计和安全评估具有重要意义。
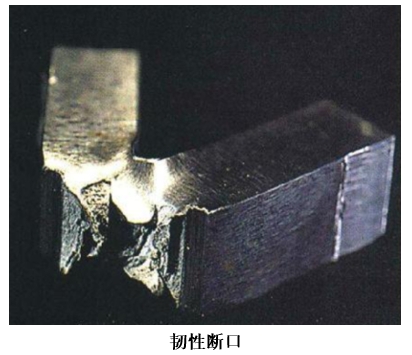
3.1 应力腐蚀裂纹
应力腐蚀裂纹(Stress Corrosion Cracking, SCC)是材料在特定腐蚀环境下,在远低于材料断裂韧性(K_IC)的应力水平下发生的裂纹扩展现象。其特征如下:
• 环境影响:应力腐蚀裂纹的形成需要特定的腐蚀环境,如海水、酸性溶液等。
• 临界应力强度因子:应力腐蚀裂纹的扩展临界应力强度因子称为K_Iscc,当应力强度因子超过K_Iscc时,裂纹会迅速扩展。
• 裂纹扩展机制:裂纹沿晶界或晶内扩展,通常为穿晶或沿晶裂纹,扩展路径取决于材料的微观结构。
• 影响因素:材料的化学成分、热处理状态、应力状态及环境介质的化学性质等都会影响应力腐蚀裂纹的形成和扩展。
• 典型案例:核电站管道、飞机机身等结构在服役过程中,因环境因素及应力作用,容易产生应力腐蚀裂纹,导致重大安全事故。
3.2 疲劳裂纹扩展
疲劳裂纹扩展(Fatigue Crack Growth)是材料在循环应力作用下,裂纹逐渐扩展并最终导致断裂的现象。其特征如下:
• 循环加载:疲劳裂纹扩展发生在材料经历反复的循环加载过程中,且应力幅值通常低于材料的屈服强度。
• 裂纹扩展阶段:疲劳裂纹扩展分为三个阶段:裂纹萌生、稳定扩展和快速失效。
o 裂纹萌生:微小裂纹在材料表面或内部的应力集中处萌生。
o 稳定扩展:裂纹以缓慢而稳定的速率扩展,此阶段的扩展速率可通过巴黎公式描述:da/dN = C(ΔK)^m,其中da/dN为裂纹扩展速率,ΔK为应力强度因子范围,C和m为材料常数。
o 快速失效:裂纹扩展速率急剧增加,直至材料最终断裂,此时裂纹扩展速率受到材料的断裂韧性限制。
• 影响因素:加载频率、应力幅值、环境条件和材料内部缺陷等因素都会影响疲劳裂纹的扩展速率。
• 检测与防护:疲劳裂纹通常通过无损检测方法(如超声波检测、X射线检测等)进行监测。材料选择、结构设计和表面处理(如喷丸处理)是防止疲劳裂纹扩展的有效手段。
• 典型案例:飞机翼梁、桥梁等结构在长时间服役过程中,常因疲劳裂纹扩展而发生断裂失效。
4断裂韧性试验
4.1测试方法
压痕法:测试试样表面抛光成镜面后,在显微硬度仪上,以10Kg负载用金刚石锥形压头在抛光表面产生压痕,并在压痕四个顶点产生预制裂纹。通过压痕载荷P和裂纹长度C计算断裂韧性(KIC)。公式如下:

其中E为杨氏模量,系统一般取300GPa。载荷P单位为N,裂纹长度C单位为mm,显微硬度HV单位为GPa。
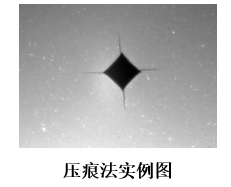
4.2取样选择
目前国内常用的断裂韧性试样有两种:
1)三点弯曲试样SE(B);
2)紧凑拉伸试样C(T)。
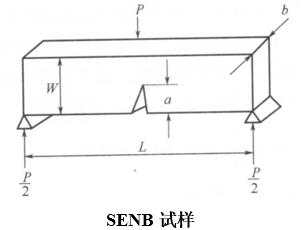
断裂韧性试验通常采用带尖锐裂纹的试样,通过直接或间接测量法监测裂纹行为。例如,用夹式引伸计测量裂纹嘴张开位移V随载荷P的变化,以评估材料抗裂纹扩展的能力及裂纹在疲劳载荷或应力腐蚀下的扩展速率。常用的断裂韧性参数包括平面应变断裂韧度K_Ic、动态断裂韧度K_Id、裂纹临界张开位移δ_c、应力腐蚀临界强度因子K_ISCC、疲劳裂纹扩展速率da/dN(毫米/周)等。I型裂纹(张开型裂纹)最易引起脆断,因此大多数断裂韧性试验都集中于I型加载。其他类型的裂纹还包括II型(滑开型裂纹)和III型(撕开型裂纹)。
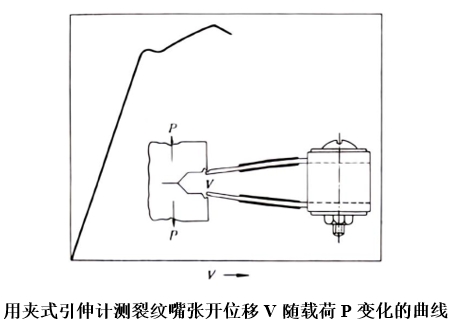
4.3试验选择
压痕法是在试样中间开一裂纹,通过三点或四点抗弯断裂测试,计算材料的断裂韧性。断裂韧性受到材料特性、试样取向、试样尺寸、应力状态、加载方式、加载速率、试验温度和试验环境等因素的影响。通常,平面应变状态、快速加载和低温会降低断裂韧性,增加脆断倾向。在实际应用中,裂纹在疲劳载荷和应力腐蚀下会缓慢扩展,直到达到临界尺寸导致断裂。因此,试验条件应尽可能接近实际工作条件。断裂韧性参数与外加载荷、试样尺寸和缺陷尺寸间有定量关系,知道其中两个参数即可预测第三个参数。这些参数可用于安全分析、事故分析、寿命估算和缺陷评定等。常用的断裂韧性试验方法有:
1. 平面应变断裂韧度 KIC 试验:适用于高强度脆性材料,KIC 越高,韧性越好。
2. 应力腐蚀临界强度因子 KISCC 试验:在腐蚀介质中,若裂纹顶端的应力强度因子 KISC 小于 KISCC,裂纹不会扩展。
3. 裂纹顶端临界张开位移 δc 试验:测量裂纹顶端塑性应变程度,δc 越高,断裂韧性越好,适用于中强度高韧性材料。

测试方法比较:
①IM法比SENB法简便经济,但测得的数据不如SENB法可靠;
②SENB法是普遍公认的标准测试方法;
③为了实际方便,要对IM法测试公式修正,使结果更接近SENB法。
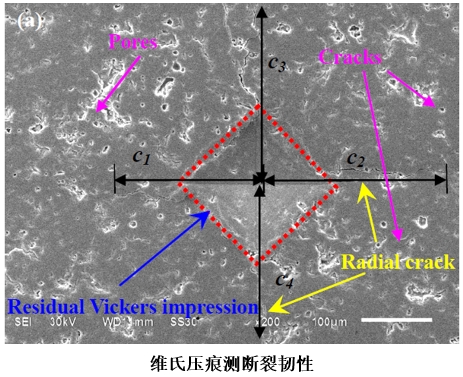
4.4断裂韧性结果分析
断裂韧性测定中的三个阶段:
1. 第一阶段:FPZ逐渐形成,应力强度因子K值单调增加。
2. 第二阶段:裂纹稳定扩展。
3. 第三阶段:K值突然减少。该现象可能由于数值方法假定理想线弹性系统,但实验进行中此假定失效,裂纹长度增加,导致大的残余CMOD。在实验初期此影响可忽略,后期影响较大。
一般仅第二阶段的断裂韧性值可用于静力分析。其平均值总结如下:
• 相对偏差均在20%以内,断裂韧性与试件尺寸无关,可获得客观值;
• 基于水平方向的相对误差,断裂韧性与MSA尺寸无关;
• 这些结果在无限制条件实验室中获得,参见1990年Saouma等人的研究结果,了解应力限制对断裂韧性的影响。
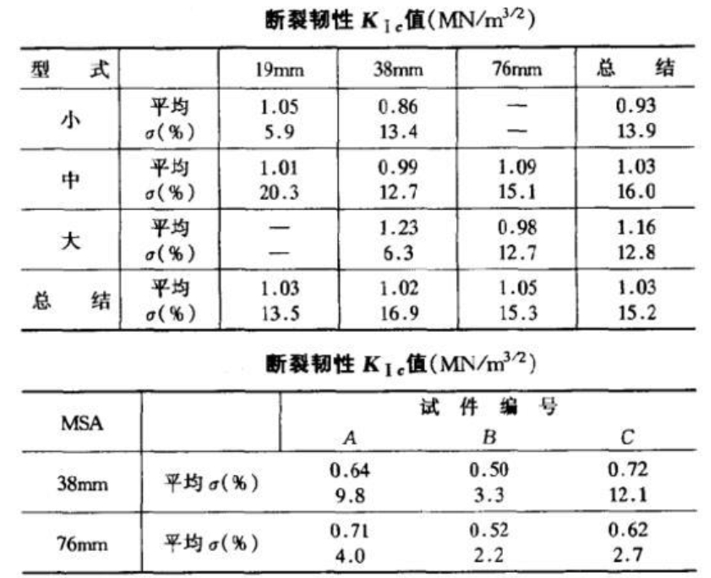
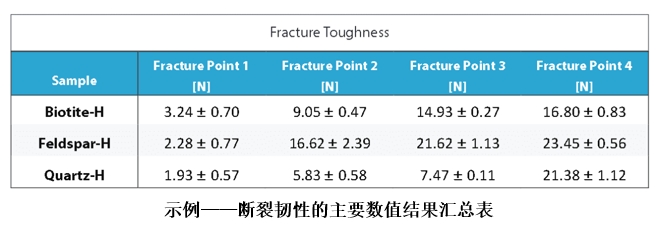
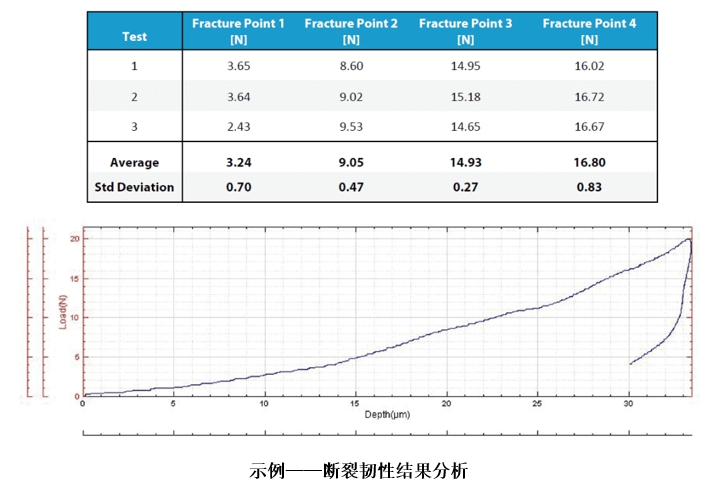