建井流程
建井流程
一、 建井工程概述
建井工程涵盖钻井、固井和完井三大环节。钻井通过机械破岩形成井筒,为油气开采奠定基础;固井通过注水泥固定套管,隔离地层、防止井壁坍塌;完井则通过射孔、安装生产管柱及增产措施,确保油气顺利开采,见图1。各环节相互衔接,确保井筒稳定与高效生产。通过毫米级精度的地下通道构建,实现从千米级地质不确定性到工程确定性的跨越,其核心技术突破体现在空间穿透、时间压缩和能量转换三个维度。现代建井技术融合了地质力学、流体动力学、材料科学、智能控制等多学科知识,其技术演进史可视为石油工业发展的缩影,其本质是通过精准的地下工程操作构建油气开采的"生命通道"。
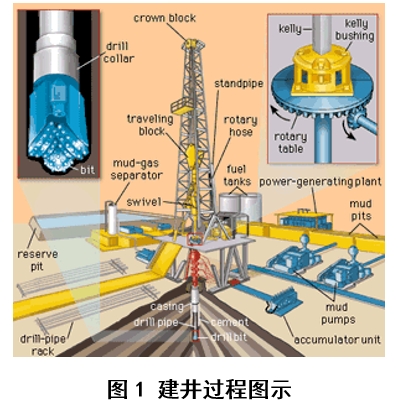
近年来,水平井长度显著增加,如2023年Permian盆地已达5700m,相较2000年增长近20倍;数字化建井显著缩短工期,如沙特Khurais油田单井工期已降至12.5天;同时,基于量子陀螺仪的轨迹控制技术提升钻进效率,降低机械比能达28%。现代建井技术演进呈现学科交叉、材料跃迁与控制范式革新三重融合趋势,如Inversion-on-the-fly算法将地震数据分辨率提升至0.5m,纳米晶金刚石复合片使钻头寿命突破300小时,Equinor的数字化钻井系统显著降低非生产时间,见图2。
国际石油公司在技术战略上形成明确路径依赖,数字化渗透率持续提升,如壳牌DrillOps系统每秒采集2TB数据,BP的电动压裂泵组降低单井碳排放37%,斯伦贝谢的AutoWell系统已实现72小时无人值守钻井。纵观技术演进史,建井工程经历了机械化、数字化和智能化三大阶段,从1960-2000年顶驱系统取代转盘钻井,使机械钻速提升170%;2000-2020年随钻测量数据传输速率从10kbps跃升至100Mbps;2020年后,机器学习算法(如DeepDrill NET)优化钻井参数,使ROP预测误差降至7%以内,标志着智能化时代的全面到来。
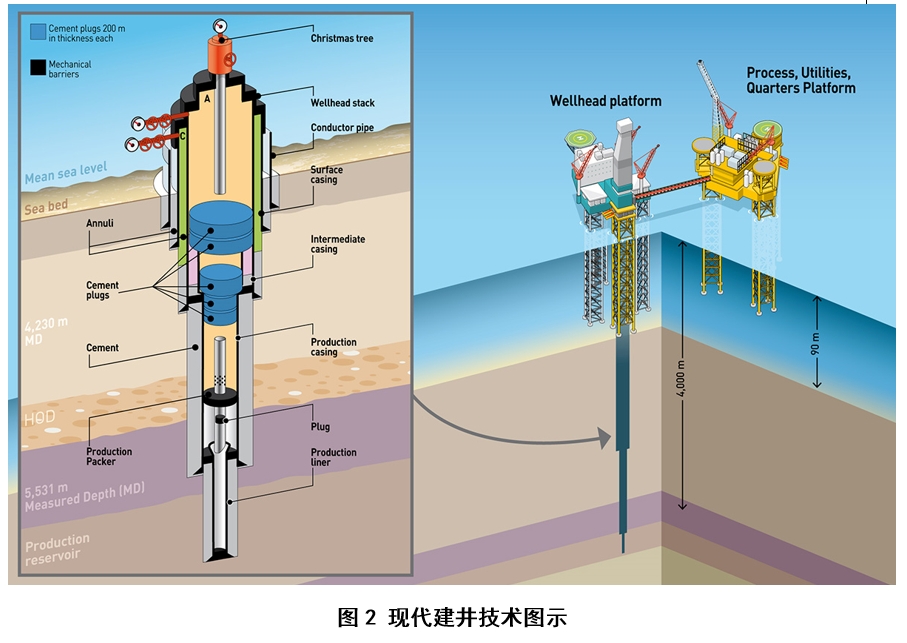
二、传统建井流程
传统建井流程的技术演进始终遵循“地质认知-工程响应-系统优化”,优化已从单纯工艺改进转向多物理场耦合的精细化控制。
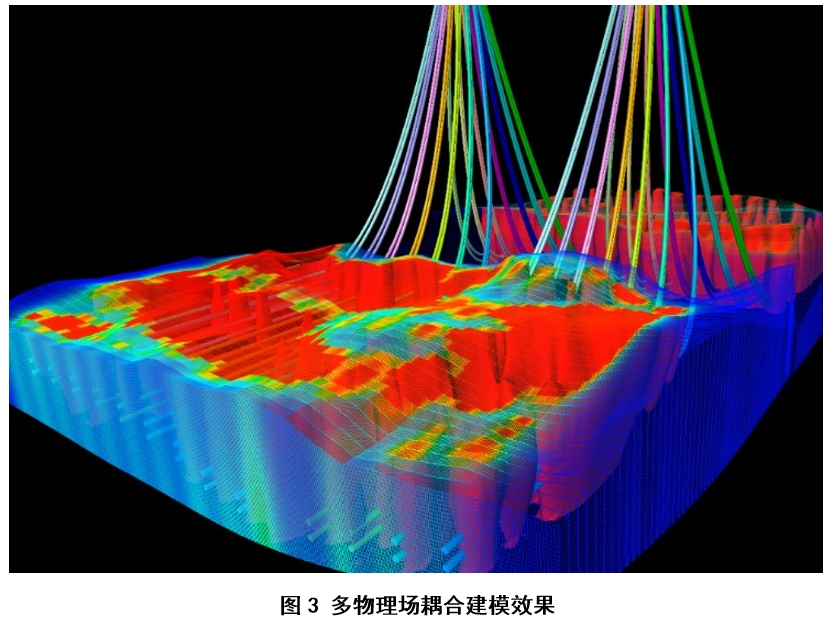
(1)钻前准备阶段
钻前准备主要包括地质与工程调查、钻井设计、设备与材料准备、场地建设与安全措施及人员组织与技术交底。首先,分析目标层位的地质条件,评估地层压力与井控风险,制定合理方案;其次,确定井身结构、钻井液体系、固井及完井方式,优化钻具组合,提高钻进效率。作业前需检查钻机、泥浆系统及井控设备,储备关键物资,并完善井场建设、安装井口装置,落实环保与安全防护措施。最后,通过合理分工、技术交底及安全培训,提升团队协作与应急处理能力,确保钻井作业顺利进行。
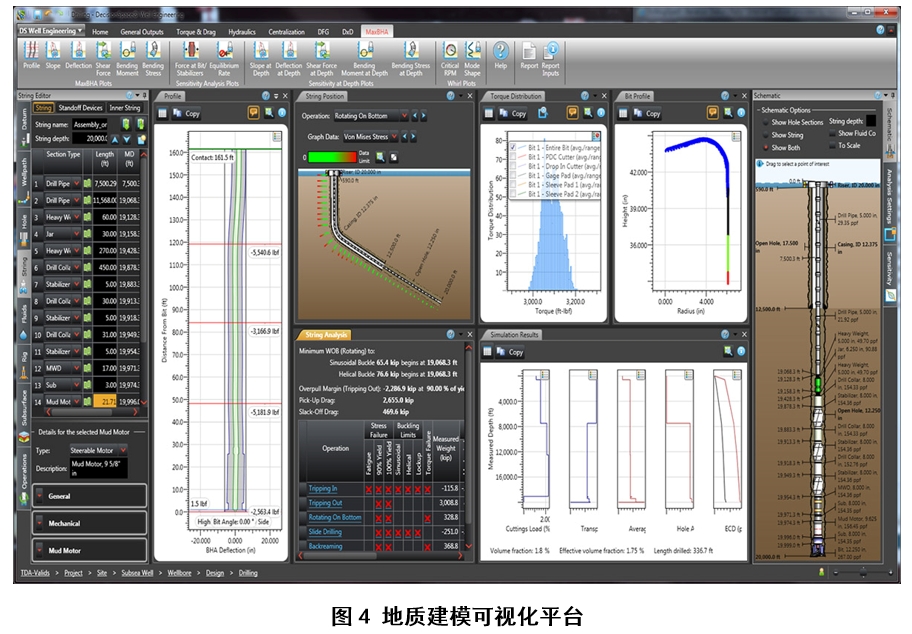
其科技突破体现在地质力学建模的数字化跃迁。以Schlumberger的Petrel平台为例,其基于全波形反演算法构建的三维地质力学模型,通过融合测井、岩心与地震数据,可反演地层杨氏模量误差小于5%。这种高精度建模使得地层压力预测突破±0.02sg的行业瓶颈,在墨西哥湾深水区块的应用中成功将井涌发生率降低37%。井眼轨迹设计方面,最小曲率法的数学本质是求解三维空间中的Frenet-Serret方程,通过引入地层各向异性张量修正井壁稳定性判据,配合钻井液当量循环密度的动态模拟,实现在页岩层段轨迹偏移量小于0.3m/100m的精准控制。
(2)钻井作业阶段
钻井作业涉及井位选择、钻井设计、井眼施工、固井及完井等过程。根据地质勘探数据确定井位,并设计钻井参数以优化钻井路径。施工过程中,通过钻头破碎岩层,并利用钻井液冷却钻头、携带岩屑、稳定井壁。钻至目标层后进行固井,以水泥封隔不同地层,防止流体窜流。随后进行完井作业,包括射孔、管柱安装及增产措施,以确保油气高效采收并投入生产,见图5。
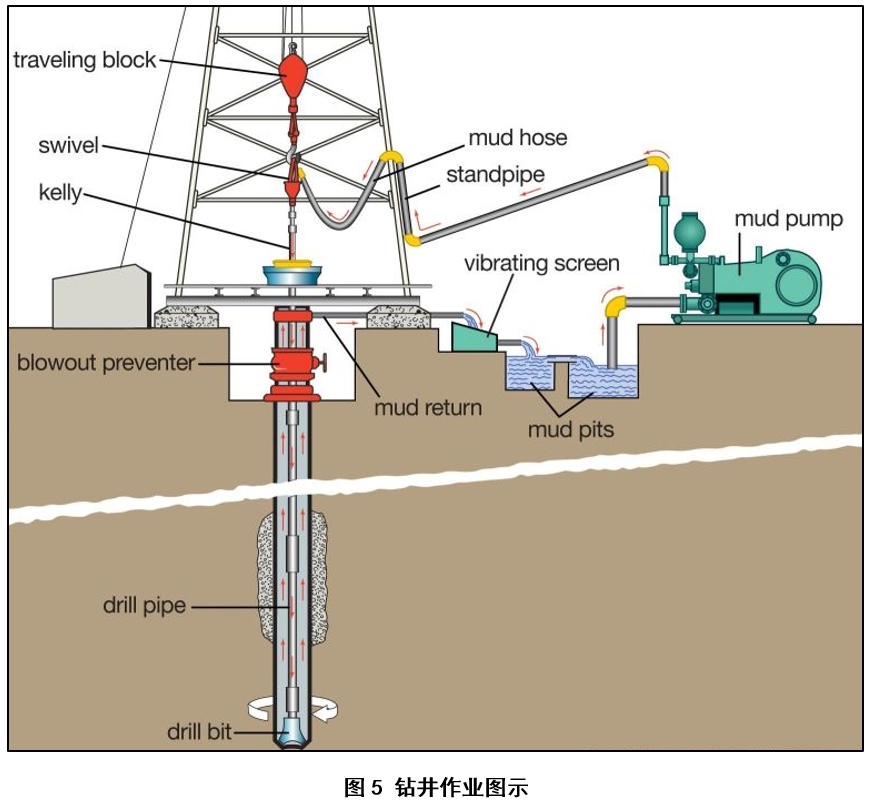
其核心矛盾在于"机械-流体-信息"三系统的协同控制。Baker Hughes的AutoTrak旋转导向系统采用闭环控制算法,其轨迹控制精度达±0.1°的背后,是井下涡轮发电机与磁阻传感器的微型化突破。哈里伯顿SpectraSphere系统的16参数实时传输,依托量子点传感器技术将伽马射线探测灵敏度提升至10nCi/g量级,配合LWD采集的声波各向异性数据,可在钻进过程中动态修正地质模型。在井控领域,动态压井法的数学模型建立在两相流Drift-Flux模型基础上,结合OLGA软件的多节点瞬态模拟,使压井作业响应时间从传统方法的数小时缩短至23分钟。
(3)固井阶段
固井是指在钻井完成后,将水泥浆注入井眼和套管之间的环空,以固定套管并提供井壁支撑。主要目的为支撑套管,防止井壁坍塌;隔离地层,防止不同层位的流体窜流(如油、水、气窜流);防止污染,避免地层水进入油层;提高井筒完整性,便于后续的完井和生产作业。主要步骤为注入水泥浆、等待凝固和质量检测,具体操作为通过管柱将水泥浆泵入环空,水泥浆凝固后形成坚固的水泥环,使用声波测井(CBL/VDL)等方法检查固井质量,见图6。
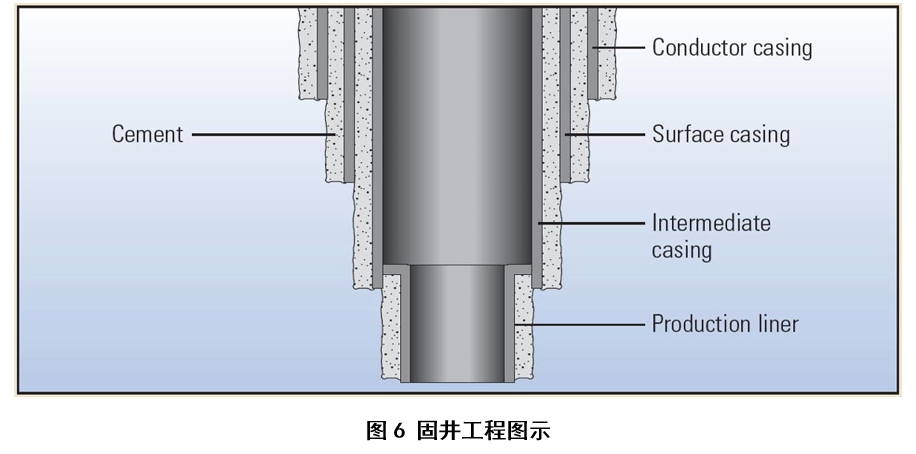
(4)完井工程阶段
完井是指在钻井和固井后,对井筒进行一系列处理,使其具备安全、高效的油气生产能力。主要目的为建立油气通道,让油气从地层流入井筒;控制产量,通过控制装置调节油气流动;保护油层,避免对储层造成损害。主要步骤为射孔、安装生产管柱、控制流体和压裂/酸化,具体操作为使用射孔枪穿透套管和水泥,使油气能够流入井筒,安装生产管柱,用于输送油气到地面,安装封隔器、节流装置等,压裂/酸化,用于提高油气流动能力,见图7。
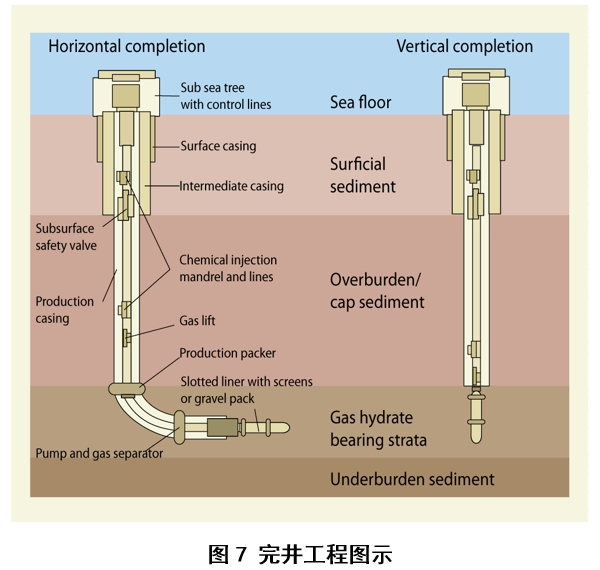
其技术发展已从"被动防护"转向"主动调控"。斯伦贝谢InForce智能完井系统的核心在于井下电动液压控制阀,其耐温等级达205℃/140MPa,通过光纤压力传感器实时监测产层贡献度,配合PID控制算法实现各产层流量偏差小于8%。水力压裂的革新体现在裂缝扩展模拟的物理机制突破,Meyer软件采用扩展有限元法耦合微地震事件反演,对裂缝网络的预测精度达到85%以上,支撑剂铺置浓度误差控制在±0.2kg/m²。膨胀式筛管的材料突破在于形状记忆合金的应用,其径向膨胀率可达200%且保持30μm的过滤精度,在渤海油田的应用中将防砂有效期延长至7年以上。
三、前沿技术
在能源转型与数字化转型的双重驱动下,全球建井技术正经历革命性跃迁。壳牌公司主导的DrillOps数字孪生系统开创了虚实融合新范式,其核心在于高精度地质力学模型与实时钻井数据的双向耦合机制。该系统通过边缘计算节点每秒处理超过2TB的随钻测井数据,利用深度学习算法(如LSTM神经网络)动态修正井眼轨迹预测模型,在巴西Libra深水油田应用中成功将轨迹偏离度控制在0.15°以内,较传统方法提升67%的调控精度。这种虚实交互的闭环控制体系,正在重新定义"钻井即服务"的产业生态。
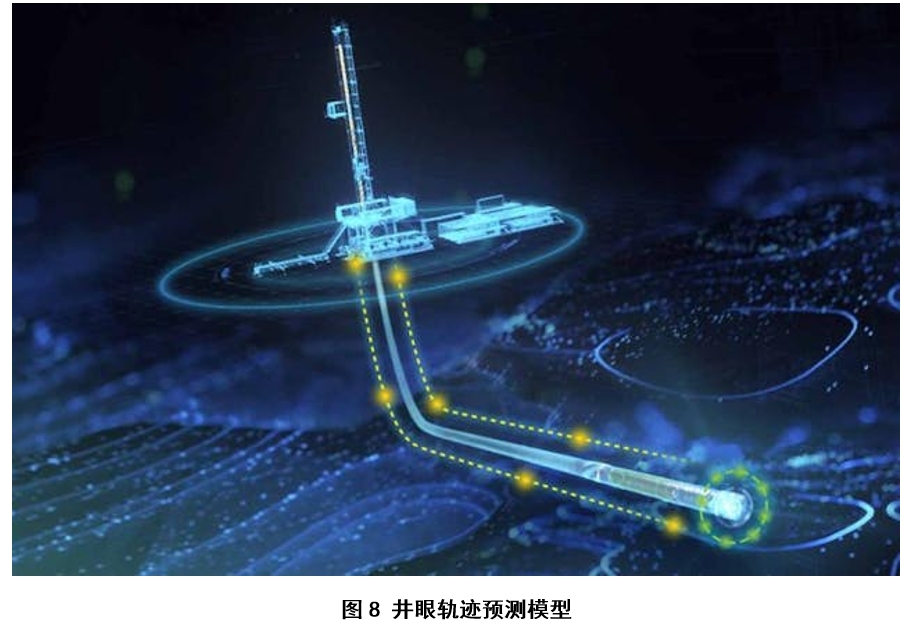
自主化钻井的突破性进展体现在NOV CyberDrill系统的参数自适应优化能力上,见图9。该系统采用强化学习框架,通过Q-learning算法在挪威北海实钻中自主完成27次钻压-转速-排量参数组合优化,将机械钻速提升至42m/h,同时将井下振动指数降低至0.3g以下。更值得关注的是石墨烯基纳米流体的工程化突破,中石油管材研究院开发的GNPD-3型钻井液通过π-π共轭作用实现纳米片层定向排列,在塔里木超深井中承受住241℃/176MPa的极端工况,其高温流变性能衰减率较常规体系降低83%。
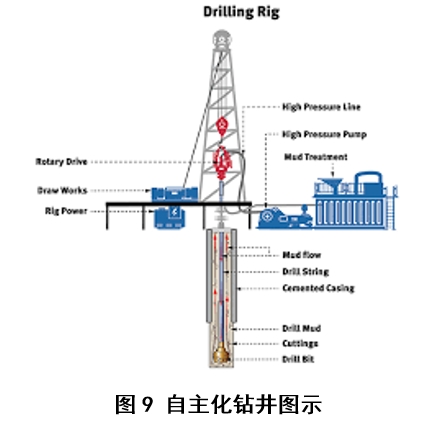
绿色建井技术正在颠覆传统作业模式。MIT联合斯伦贝谢研发的激光-机械复合钻头采用飞秒激光剥蚀机理,在二叠纪盆地试验中实现单趟钻进尺提升至580米,单位进尺能耗降至1.8kWh/m,见图10。雪佛龙的CO2泡沫压裂技术通过超临界相态调控,在二叠纪盆地Wolfcamp页岩形成平均缝宽0.63mm、导流能力达1200mD·cm的复杂裂缝网络,支撑剂嵌入深度减少45%。数字岩心技术的突破则体现在多尺度建模能力上,埃克森美孚开发的DCRx平台结合μCT扫描(分辨率达0.65μm)与格子玻尔兹曼模拟,成功预测鹰滩页岩纳米孔喉内吸附态甲烷的扩散系数(2.1×10⁻⁹ m²/s),该模型已被纳入UNCONG软件作为行业标准算法。
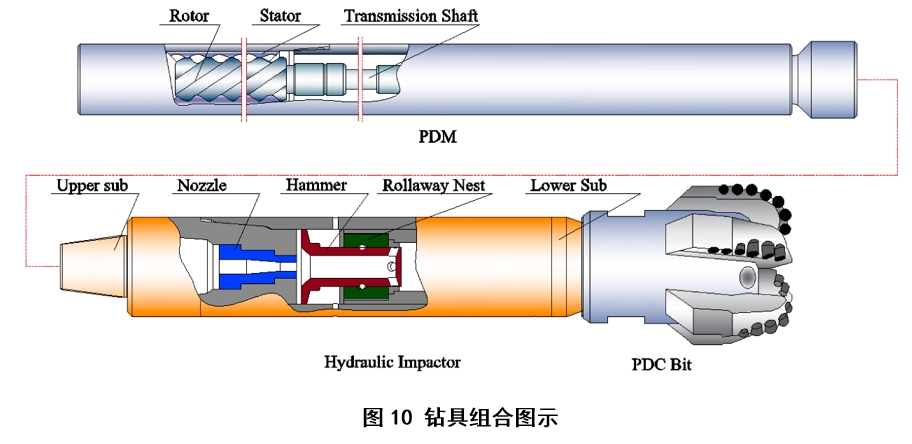
极端环境建井技术正在突破地球物理极限。Transocean的深水双梯度钻井系统采用海底泵注与智能隔水管耦合控制,在墨西哥湾3000m水深作业中将环空压力波动控制在±0.03sg范围内,其关键创新在于基于CFD-DEM耦合算法的多相流控制模型。冰岛深钻项目(IDDP-3)将油气井高温合金技术移植到地热领域,采用TaC增强型镍基合金钻头在岩浆房边缘(450℃)完成持续钻进,该项目揭示的花岗岩热-力-化耦合损伤机制为超高温钻井提供了全新理论框架。挪威Northern Lights碳封存项目部署的ΦOTDR光纤传感网络,通过布里渊频移解析实现了CO₂羽流运移的4D成像监测,其空间分辨率达1m、温度灵敏度0.01℃。
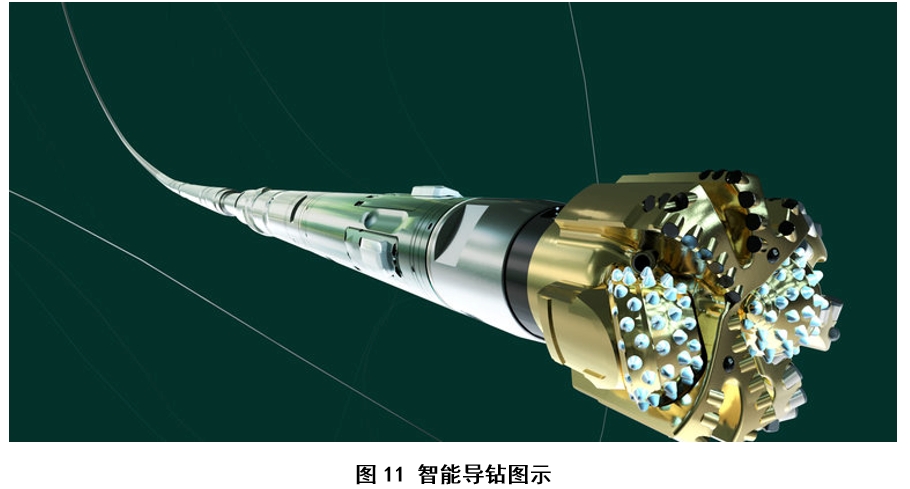