水力旋流器
水力旋流器
1.水力旋流器的概念
水力旋流器是一种连续作业的分级设备,是选矿工业中最重要的设备之一,在选矿中主要用作分级设备,尤其在细粒分级作业中极为有效。其利用离心力来加速颗粒的沉降速度,通常与磨矿机组成磨矿分级闭路流程,分级效果对磨矿流程的效能有着非常重要的影响。它广泛用于闭路磨矿作业,但也可用于脱泥、除砂和浓密等其他作业。
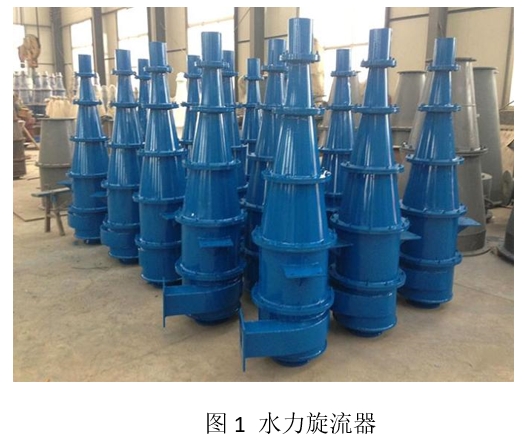
水力旋流器在石油行业同样发挥重要作用,水力旋流器是油气田开采过程中净化处理的基础应用设备,主要应用在油田开发中后期含水量较高阶段。在油田开发过程中,在不同时期都会经历含水的逐步提升,原油见水早,含水率增长速度快。稳产开发期,油田原油含水率达到60%~70%,开发后期原油含水率高达90%以上。然而,在输送过程中,原油含水变大成为了危害。例如,对相应处理液量增加,降低管道、设备的有效利用率;增加输送过程的动力消耗;引起管道与设备的结垢和腐蚀。对于海上油田,生产水来源于在油气开釆过程中所产出的地层伴生水、钻井液和洗井液污水,其中以油气生产过程中产出的地层伴生水为主。经过处理的生产水在达标的情况下,其通常的方式是回注地层或者对外合规排放至海洋中,所以务必要对生产水进行油水分离、净化,以达到排放的标准。
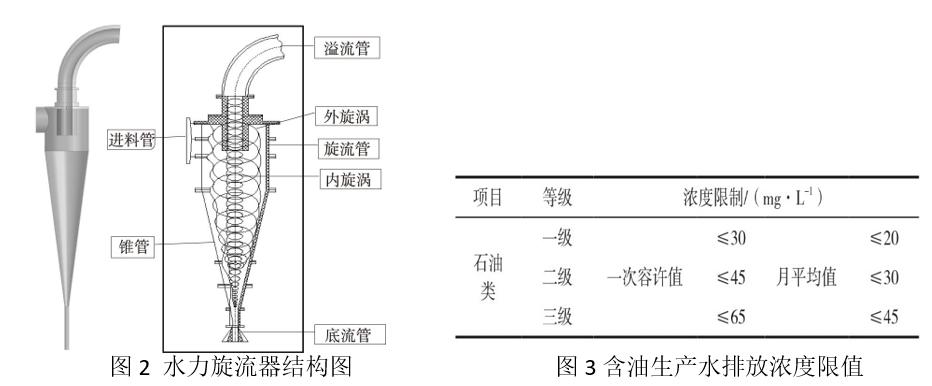
水力旋流器可用于油、水分离。它与传统的游离水脱出器、重力沉降、气浮选电水等设备相比,具有结构简单、体积小、重量轻、没有运动部件、分离效率高和处理时间短等特点,是一种新型、高效、节能的分离设备。
2.水力旋流器的结构及工作原理
水力旋流器是一个外形较长,内部装有圆锥形筒的压力容器,其主要部件有:壳体、旋流管、支撑板、固定板、底流口、溢流口等。一般的水力旋流器如下:水力旋流器利用两种液体的密度差,借助于离心力,使油滴从水中分离出去。生产污水由入口1处进入 ,在圆锥筒内旋转形成旋流。其离心力足以使油水分离,密度较大的水及固体颗粒靠近管壁而密度较小的油则集中到中心部位。中心部位为低压区,水相在管壁连续旋转,由于截面积逐渐减少,最后水及固体颗粒从细口端4排出,而油则沿中心线从粗口端5排出。
;变形扭矩是由套管和管箍变形产生的。由于在整个上扣过程中,变形扭矩远小于摩擦扭矩,因此可忽略变形扭矩的影响,仅将摩擦扭矩作为总上扣扭矩。总上扣扭矩计算公 式如下:
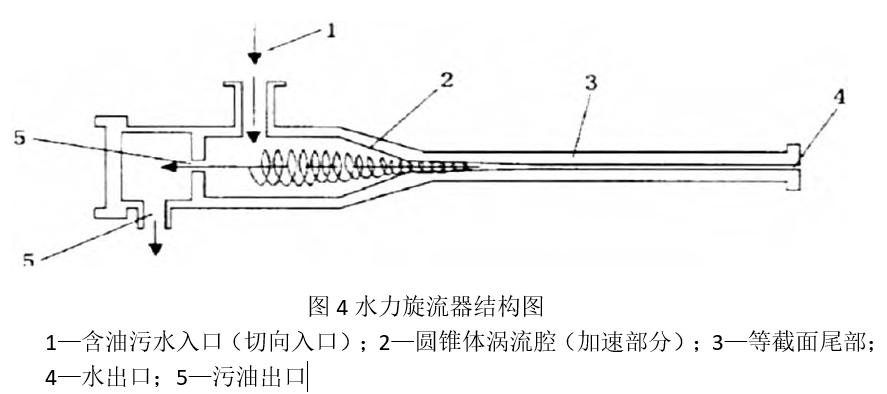
水力旋流器各段作用如下:
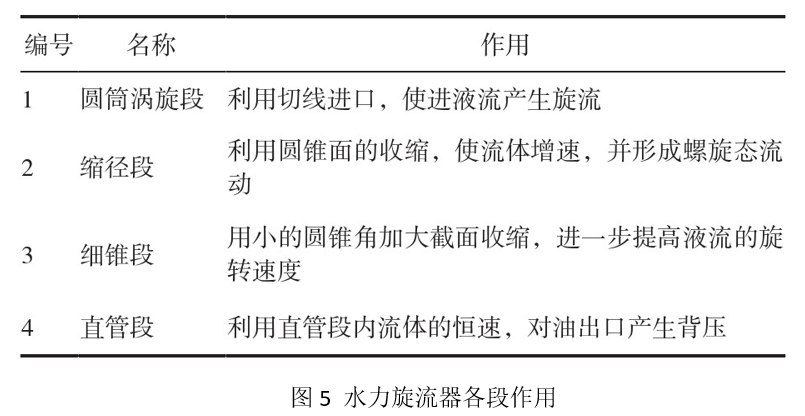
根据处理量大小也可以选择多个水力旋流器并联方式来加大处理量,中海油某油田就是多个并联同时使用。
旋流器分离原理:混合物料从进料口受到入口压力及重力影响驱动沿切线方向进入水力旋流器,在旋流器的内部,有一个由上往下的旋转流,依照不同成分的浓度和颗粒大小,将其分成外旋流和内旋流。
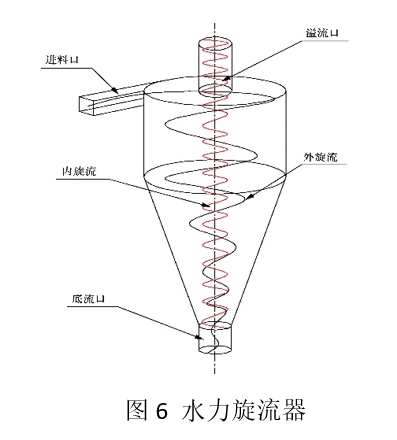
假设在流场半径为r处的微元体宽、厚分别用dr和dz表示,于是,基于一致的水平面,对重力势能进行忽视,可得伯努利方程如下:

3.水力旋流法处理效果的主要影响因素
3.1控制适当的入口流量
水力旋流器分离效率随流量的增大而增大,増大到一定程度后,反而使分离效率降低,其原因是过高的流速下,将发生油滴破碎,产生更难分离的微小油滴。可以根据实际情况关停一台或多台水力旋流器,确保足够流量的污水进入在线的水力旋流器处理。
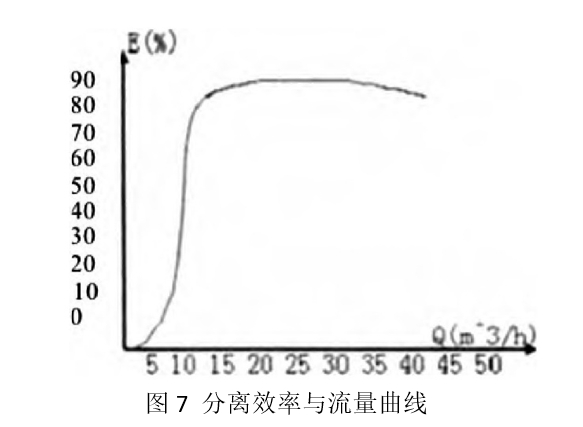
3.2保证旋流器高效的压差比
差压比是通过控制出口管线上的控制阀控制,来调节油、水出口的压力,以此实现一个让油水旋流起来的差压比。差压比太小,分离效率减低。差压比太大,将导致对后续生产水处理系统产生不必要的负荷。据实际生产经验,差压比通常在1.7~2.2之间,经济效益达到最高。
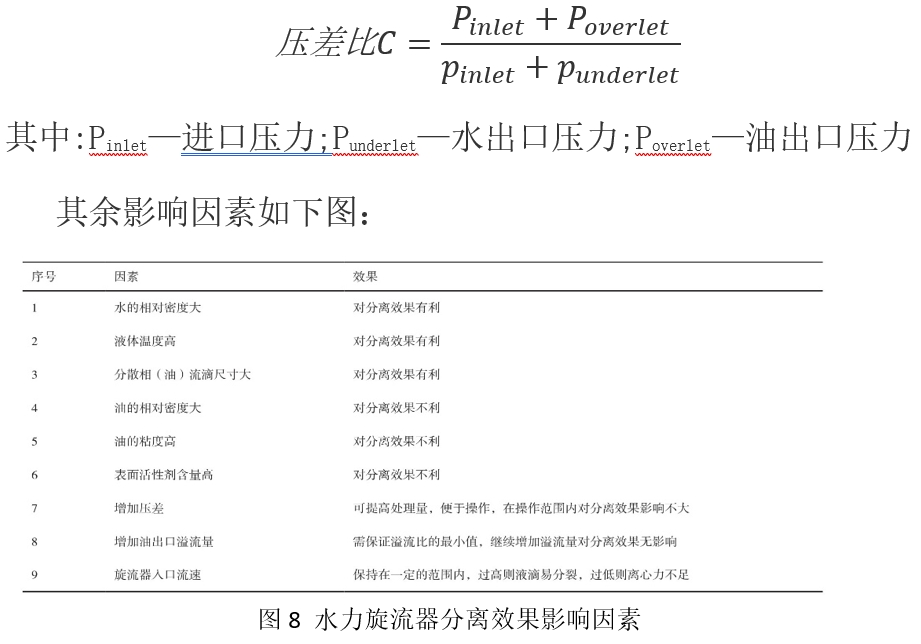
4.水力旋流器的国内外发展现状与种类
井下水力旋流器同井注采油水分离装置的研究始于20世纪50—60年代。近年来,对于井下水力旋流油水分离装置的研究主要是在:入流口的方式(径向进流或轴向进流或混入式)、锥段的锥角大小与锥形结构、底流口与溢流口是否在同侧等方面。常见的径向进流双锥形水力旋流器如图9所示。入口是混合液的进入口,溢流口为脱水后的出油口,底流口为出水口,大、小锥段是混合液的旋流空间。
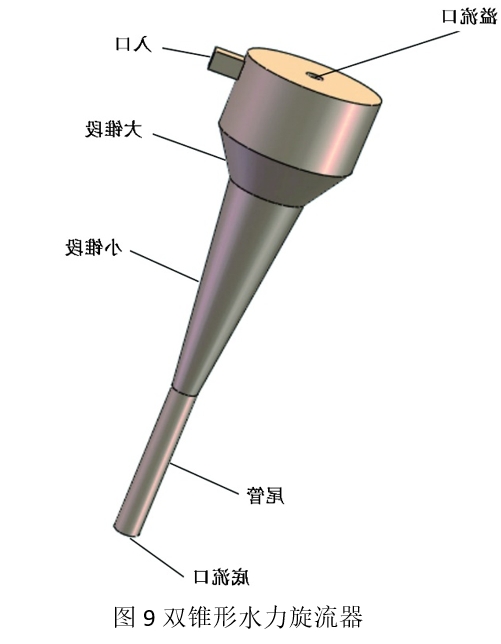
水力旋流器可分为静态和动态水力旋流器,但动态水力旋流器与静态水力旋流器相比,能够更好地从水中分离出更小的油滴、具有更低的入口压力。所以对于井下油水分离水力旋流器而言,动态水力旋流器更有优势。曾涛等以三相旋流器、动态旋流器、气浮旋流一体化分离装置为研究对象对水力旋流器在油田采出液应用进展进行研究。赵宗昌等通过设置预旋喷嘴使转动式油水分离水力旋流器的分离效率与静止式相比显著提高。Petty等设计的一种双入口和双出口水力旋流器用于井下油水分离,与锥形分离器相比,油水混合液的处理量增大,但存在结构较大、不紧凑等问题。Klasson等研究并设计了一种通过马达转动的井下动态旋流器用于油水分离。
杨晓惠设计轴流导叶式水力旋流器井下油水分离系统,与采用切入式水力旋流器的常规井下油水分离系统相比,该系统具有能耗低、结构紧凑、径向尺寸小等特点。杨树人等为实现高含水油井同井注采工艺,根据与多杯等流型气锚相似分离原理优化设计出一种多杯等流型油水分离器,其结构如图10所示。
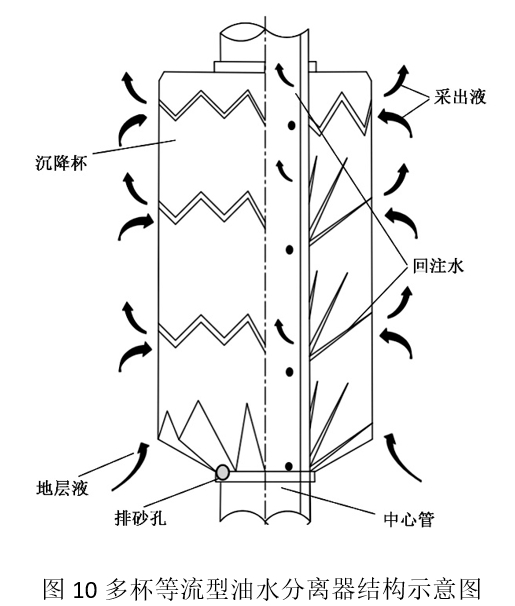
中外学者利用计算流体动力学仿真分析和物模实验对水力旋流器进行结构与参数的优化设计。张瑞霞等利用相似准则设计出一种旋流器分离器,并选择典型的旋流器模型对该井下旋流油水分离器进行研究。赵立新等基于现有油水分离的研究成果,提出了一种同向出流倒锥式旋流器,运用FLUENT软件分析了旋流器的典型结构参数(溢流管直径、溢流管伸入长度、锥角和出水口尺寸)对其分离性能的影响。Yin等在三维稳态假设下对全尺度油水旋流器进行了建模和模拟分析。等对井下油水分离装置(图11)进行优化设计,采用计算流体动力学来计算每种特殊情况下的底流油浓度,并分析了优化前后的分离性能变化,对不同的流速下新型轴向水力旋流器(图12)分离性能影响参数进行数值模拟研究。
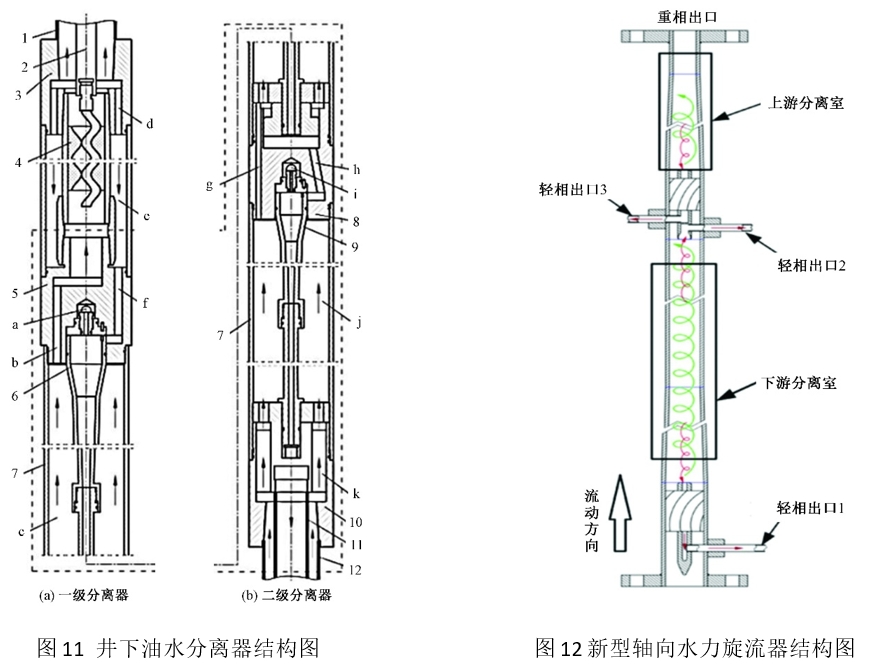
近年来,研究者们倾向于结合叶轮叶片而组装的动态旋流器,图13为动态水力旋流器结构。于哲和张晟提出的循环式中心进料动态水力旋流器合理利用了旋流发生叶轮的结构特性,使进料液直接流入叶轮中心。由于叶轮中心的绝对低压,进料压力会随叶轮转速的增大而减小,从达成了设备的自吸性,使电动机和供油水泵的负载得以缓解。
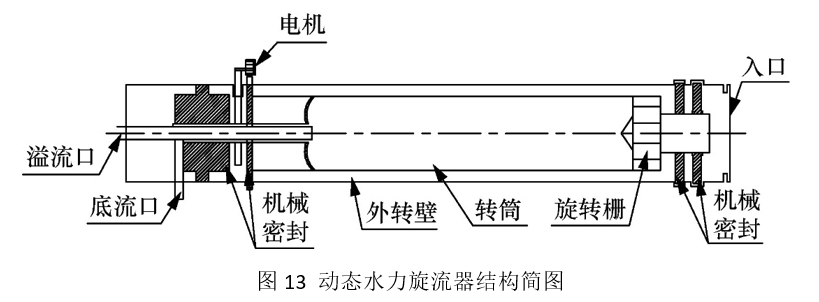
目前中外对动态旋流器的研究比较广泛,随着动态旋流器在油田上的应用,动态旋流器设计应用方向从最初的转动式外壳向内部增设旋转叶轮或旋转叶片转变,现如今研究者们普遍热衷于通过仿真手段结合实验探索获取更好的动态旋流器内部流场。
在油气田开发中钻井液处理、分离伴生气、含油水处理脱泥脱油等对三相要求同时分离,加快了单一传统的两相旋流分离器向三相旋流分离器的发展进程。在分离含有伴生气的油田采出液介质时,三相旋流器也有很大的应用空间,目前主要的结构设计是在气-液-固三相旋流器的结构上进行改进以及新型的内锥式旋流器。
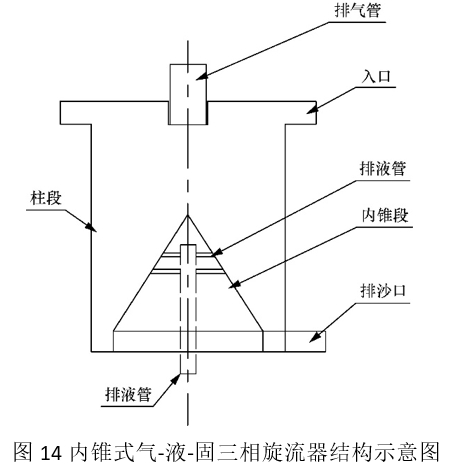